Electronic Component Procurement Guide – How to Source Every Part
As technology advances each year, so does the complexity of electronic designs. For the engineer, selecting components can be a major research project— checking material specs, checking data sheets, and sizing the right fit for the assembly.
For the procurement agent, the job's a simple matter of finding the cheapest available source, right? … Right?
Too many sourcing departments at OEMs and other product makers are overlooking the many factors and hurdles in getting the best results possible. Those results must work for not only your budget, but also the product designers and the production team.
Fortunately, with some basic education, you can understand the significance of product specs on your opponent choices. From there, you can have meaningful dialogue with the engineering team and your own department.
This ambitious guide aims to supply you with a guide to every major electronic component in your procurement journey. We'll provide both general and product-specific sourcing tips.
If you want to skip ahead, click on a section below:
Product-specific tips:
PART 1: General Procurement Tips for Electronic Components
Any sourcing job has a few general criteria to watch for, regardless of component type. Some of them are obvious, others not so much:
- Quality
- Availability
- Application fit
- Standards and regulations
- Warranty and support
- Cost
Quality
This is the one your engineering team will care most about. Bad actors can cause:
- Circuit failure
- Poor performance of assembly
- Damage to equipment
- Danger to humans
Part quality problems most often come from:
- Bad batches: Variations in the manufacturing process can lead to inconsistencies across production runs. A poor-quality batch could result in circuit instability or shoddy performance.
- Counterfeits: The internet is a sea of low-cost fake parts that often compromise on quality. Accidentally ordering these imposters can lead to circuit failures and safety hazards.
- Obsolescence: Discontinued parts don't magically disappear the moment the manufacturer ends last-time buys. Using outdated components still on the market can render your design obsolete, affecting the performance and useful life of your product.
Availability
The waiting game isn’t fun, and it’s easy to lose.
Make sure the electronic components you’ve honed in on are available in the necessary quantities. Sometimes small-order lead times are short. Don't assume you'll get the same speed when you make a bigger order, even if it's the same part and manufacturer.
Order early and often if the parts are:
- Obscure
- In-demand
- Heading toward obsolescence
This approach makes replacements and expansions straightforward, limiting downtime and costly redesigns.
Another, more design-focused approach to shortages is substituting in an alternative part that offers similar functionality. You certainly shouldn’t throw safety or quality out the window, but settling for “close enough” might get your project out the door months sooner.
Tip: If your components tend to play hard-to-get, enlist the services of a distributor. Unlike a single buyer, a distributor has an extensive supplier network and a constant finger on the pulse of market changes.
Application Fit
If you’re building equipment whose failure could cause the loss of human lives or million-dollar machinery, don’t instinctively buy the cheapest wire or circuit protector.
When picking components, think about where and how your team will use them. For example, the intense heat of industrial furnaces or the freezing conditions in transportation refrigeration call for parts that can thrive in the extreme. In an energy facility with nonstop vibration, the components need to be mechanically tough.
It’s also important that any new components play nicely with your current system. Talking to product experts or using simulation tools to see how your choices might hold up can save you headaches and money later.
To sum it up: Match your investment to the level of electrical performance, flexibility, and size you need. The results will be more durability and less upkeep – for both the part and the assembly.
Standards & Regulations
The importance of certifications and standards largely depends on your use case and industry. Chances are you already have some marching orders for compliance – we’re talking about electricity, after all.
Electronic component standards usually account for:
- Safety
- Reliability
- Durability
If your company isn’t comfortable with selecting compliant parts, talk to an experienced distributor. If you can’t trust the component to do its job, how can you trust the full assembly to do its job?
Warranty & Support
This concept isn’t much different from a commercial electronic product like an iPhone. A warranty should reflect the maker's confidence in its product's durability and performance.
An electronic component purchase with a good warranty offers more peace of mind than a bad warranty or none at all. When sourcing electronic parts, weigh the importance of the component vs. the manufacturer’s warranty:
- Length – Reduces risk of incurring additional costs for replacements or repairs
- Coverage – Some warranties may cover only parts, while others include labor and even replacement services
- Terms – May include limitations on usage, environment, or maintenance requirements
Don’t forget your needs after the parts arrive. If your own operation lacks experience with the type of parts you need, check out the maker’s level of tech support. In big projects, after-sale services can soften the integration’s impact on your schedule. Give bonus points to sellers with full training resources and a maintenance program.
Cost
We were sneaky and waited until the end to include this.
Why? Because you already know upper management wants you to find cost-efficient parts.
Actually, there’s another reason: Too often, procurement specialists go for the cheapest component possible. This short-sighted strategy may introduce into your design:
- Counterfeit parts
- Low-quality parts
- Parts that aren’t the best fit for your application
All of these mistakes can result in having to reorder parts, rework designs, and redo the production stage. These “re-”s in turn lead to:
- Downtime
- Delayed launch
- Extra testing
- Poor reputation with customers
If that happens, guess what your short-term “savings” got you? More long-term cost.
Thinking long-term means accounting for all factors of purchase cost:
Up-Front Cost
Depends on type, quality, features, size, & availability
Installation Cost
Labor and equipment for learning, mounting, wiring, & calibrating
Operation Cost
Energy use, processing power, & communication bandwidth
Maintenance Cost
Repair, recalibrating, & cleaning routinely and on-demand
Most major manufacturers’ products come with a hefty price tag. You’ll have to decide whether the quality is worth the cost – for today and 5 years from now.
PART 2: Component-Specific Tips for Electronics Procurement
Each electronic assembly contains a variety of tiny components, each with its own functions, needs, and considerations. A trait that's irrelevant to one project might be critical to another.
Below are overviews, key selection criteria, and links to more detailed explanations for all the major components. along with links to more detailed explanations. To skip to a certain component, click on a list item here:
- Cable & Wire
- Cable Management
- Labels
- Circuit Breakers
- PLCs
- Relays
- Sensors
- Terminal Blocks
- Vehicle Lighting
Cable & Wire
Top Criteria for Industrial Cable & Wire | |
Mechanical durability | Heat, flame, & cold resistance |
Shielding | Corrosion resistance |
Size | Processability |
Flexibility |
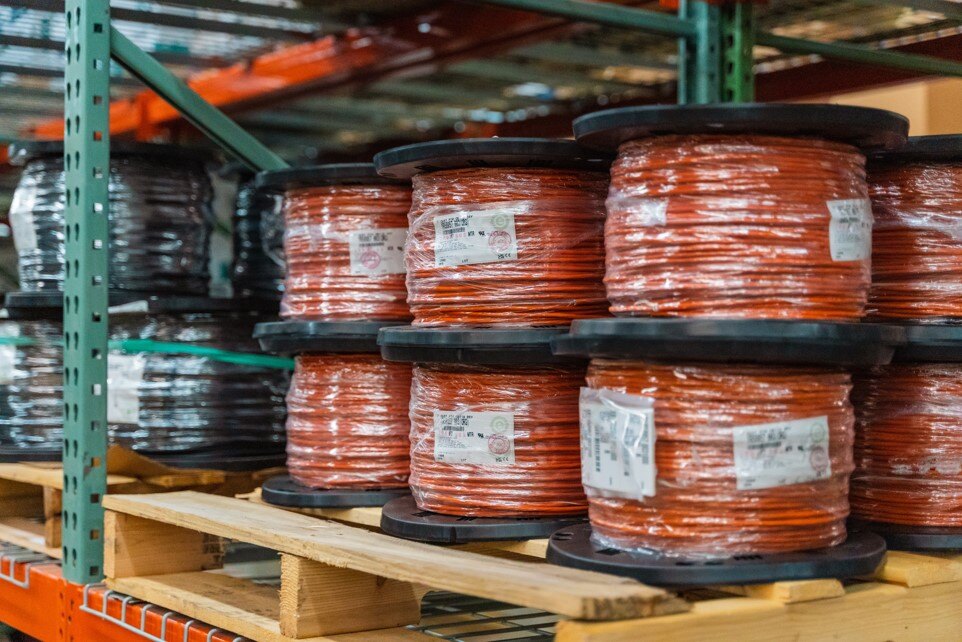
Top suppliers:
Overview of Cable & Wire Sourcing
While intricate layouts and fancy technology can make a product design sing, industrial cables and wires are just as crucial to performance, safety, and durability.
With an absurd amount of variety available, it can be overwhelming to browse a manufacturer’s e-store.
Several factors contribute to the durability of a wire assembly, including its diameter and protective coatings. Today’s customers are demanding smaller and smaller designs, which makes the physical side of cable performance more challenging to manage.
Will your cables be at risk of being stepped on, run over, or cut? Two traits to watch out for are crush and cut-through resistance.
- Crush resistance – Use jacketing/insulation made of polyethylene, Neoprene, nylon, or thermoplastic rubber. Stick to steel conductors, fillers, & armoring.
- Cut-through resistance – Use jacketing/insulation made of nylon, TPE, fluoropolymers, or XLPE. Try nickel-plated conductors, polyimide tape fillers, & steel armoring.
Gauge matters to electrical performance, as thicker cables generally have lower resistance and can handle higher electrical loads across long distances. Select a gauge that can safely carry the current your application requires without overheating or losing voltage.
Length is important too, but for more than just physical spacing of its connection points. A cable’s signal decreases as it travels, making excessively long cables a poor fit for applications that need low losses.
At the same time, your project may call for a cable with some mechanical flexibility. This means the product is usable in tight spaces without snapping due to bending stress.
Overview of Cable & Wire Sourcing
While intricate layouts and fancy technology can make a product design sing, industrial cables and wires are just as crucial to performance, safety, and durability.
With an absurd amount of variety available, it can be overwhelming to browse a manufacturer’s e-store.
Several factors contribute to the durability of a wire assembly, including its diameter and protective coatings. Today’s customers are demanding smaller and smaller designs, which makes the physical side of cable performance more challenging to manage.
Will your cables be at risk of being stepped on, run over, or cut? Two traits to watch out for are crush and cut-through resistance.
- Crush resistance – Use jacketing/insulation made of polyethylene, Neoprene, nylon, or thermoplastic rubber. Stick to steel conductors, fillers, & armoring.
- Cut-through resistance – Use jacketing/insulation made of nylon, TPE, fluoropolymers, or XLPE. Try nickel-plated conductors, polyimide tape fillers, & steel armoring.
Gauge matters to electrical performance, as thicker cables generally have lower resistance and can handle higher electrical loads across long distances. Select a gauge that can safely carry the current your application requires without overheating or losing voltage.
Length is important too, but for more than just physical spacing of its connection points. A cable’s signal decreases as it travels, making excessively long cables a poor fit for applications that need low losses.
At the same time, your project may call for a cable with some mechanical flexibility. This means the product is usable in tight spaces without snapping due to bending stress.
Types of Industrial Cable & Wires
Given the complex needs of industrial assemblies, the vendor often has to correct the purchaser on the best cable type for their application. Even project engineers who don’t specialize in wiring can benefit from expert recommendations.
Pros | Cons | Use Cases | |||||||
Single-Conductor Cables |
|
|
Prototyping & development at high voltage | ||||||
Multiconductor Cables |
|
|
Complex setups; areas with cross talk or mechanical hazards; data transmission; A/V | ||||||
Twisted Pair Cables |
|
|
Telecoms, data centers, sound engineering | ||||||
Ethernet (Cat) Cables |
|
|
Computers, network devices, automated machinery | ||||||
Coaxial Cables |
|
|
TV, internet, radio, data transmission | ||||||
Fiber-Optic Cables |
|
|
Datacom; transportation; military; oil, gas, & mining | ||||||
Ribbon Cables |
|
|
Transmitting sensitive signals over long distances |
Once you know which industrial cable type you need, the next step is matching your application to a specific material and product. Some categories of cables serve dedicated purposes.
Power cables connect electrical equipment and machinery to power sources. Control cables transmit signals between devices and automated systems. Communication cables transmit data and signals throughout networks, connecting computers, PLCs, and other devices. And instrumentation cables send data recorded by sensors and measuring instruments.
Cable Management Products
Top Criteria for Cable Management Products | |
Organization | Heat, flame, & cold resistance |
Strength | Corrosion resistance |
Size | Installation & maintenance |
Flexibility |
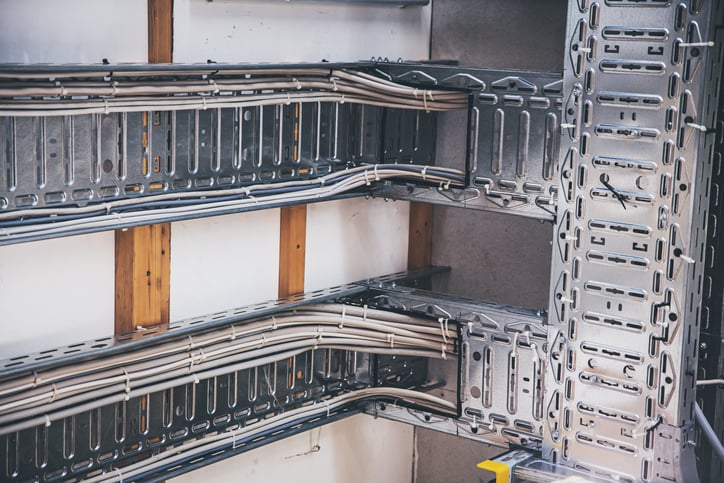
Overview of Cable Management Sourcing
At the heart of any great cable assembly, you’ll see great industrial cable management. At a well-organized data center, for example, you'll find carefully arranged paths that guide and protect cables as they traverse the building. These components are not just about keeping cables out of sight; they’re also crucial for:
- Preventing damage
- Reducing interference
- Boosting accessibility for maintenance & upgrades
As for the physical traits, size matters in both length and gauge.
- Gauge determines the maximum cable capacity and protection level.
- Length dictates how much cable the product can manage without additional connectors.
Not only must the product’s size fit within the initial installation area; it should also support any modification and expansion the user wants down the road. Larger cable management products may increase initial cost, but the reduction in long-term maintenance might be worth it.
Types of Cable Management Solutions
You could say there are two types of cable management products in this world: those that are conduits, and those that aren’t. Of course, there are nuances – cable trays, ties, wraps, and ducts aren’t technically conduits, but they serve the same role: organizing and protecting your system.
Type | Pros | Cons | Use Cases | ||||||
Ties & Wraps |
|
|
Temporary setups and light-duty applications; managing cables in offices or homes | ||||||
Trays |
|
|
Industrial settings for heavy cables; assemblies with frequent maintenance; high-volume commercial projects | ||||||
Ducts & Raceways |
|
|
Commercial buildings to conceal and manage cables safely and aesthetically | ||||||
Conduits |
|
|
Permanent construction; exposed systems facing external damage risks |
Cable ties are simple fastening devices, typically made from plastic. They’re not structural and don’t provide a pathway for cabling. However, industrial cable ties can still maintain a semblance of neatness in the right setup, especially temporary ones.
Cable wraps are flexible sleeves made from fabric, neoprene, or Velcro. As you’ve probably figured out, they wrap around cables to keep them organized. They’re often lumped together with cable ties because both options are quick-and-easy solutions that don’t offer much physical support. The main difference is that you can adjust a protective sleeve without destroying it.
Cable trays are open, rigid structures that support and hold cables in place. Despite being a structural component, trays don’t fully enclose and protect the wires inside them. Industrial cable trays are only usable with certain cable types, per Article 392 of the National Electric Code.
Cable ducts are enclosed tubes with a removable cover so you can lay cable inside along the pathway. Ducts can consist of metal or plastic and often feature a segmented design.
Cable raceways look and function similarly to ducts, but they include an open channel or trough for accessibility. From there, you can leave the raceway covered or uncovered, opening it as necessary for changes. The extra usability comes at the cost of less protection.
Cable conduits are a specific type of tubing or enclosed channel made of metal or plastic. They can be either rigid or flexible. These products are where the buck stops if you need to comply with safety requirements.
Cable & Wire Labels
Top Criteria for Cable Management Products | |
Mechanical durability – Abrasion & tear resistance | Heat, flame, & cold resistance |
Readability | Corrosion resistance |
Location – Before or after termination |
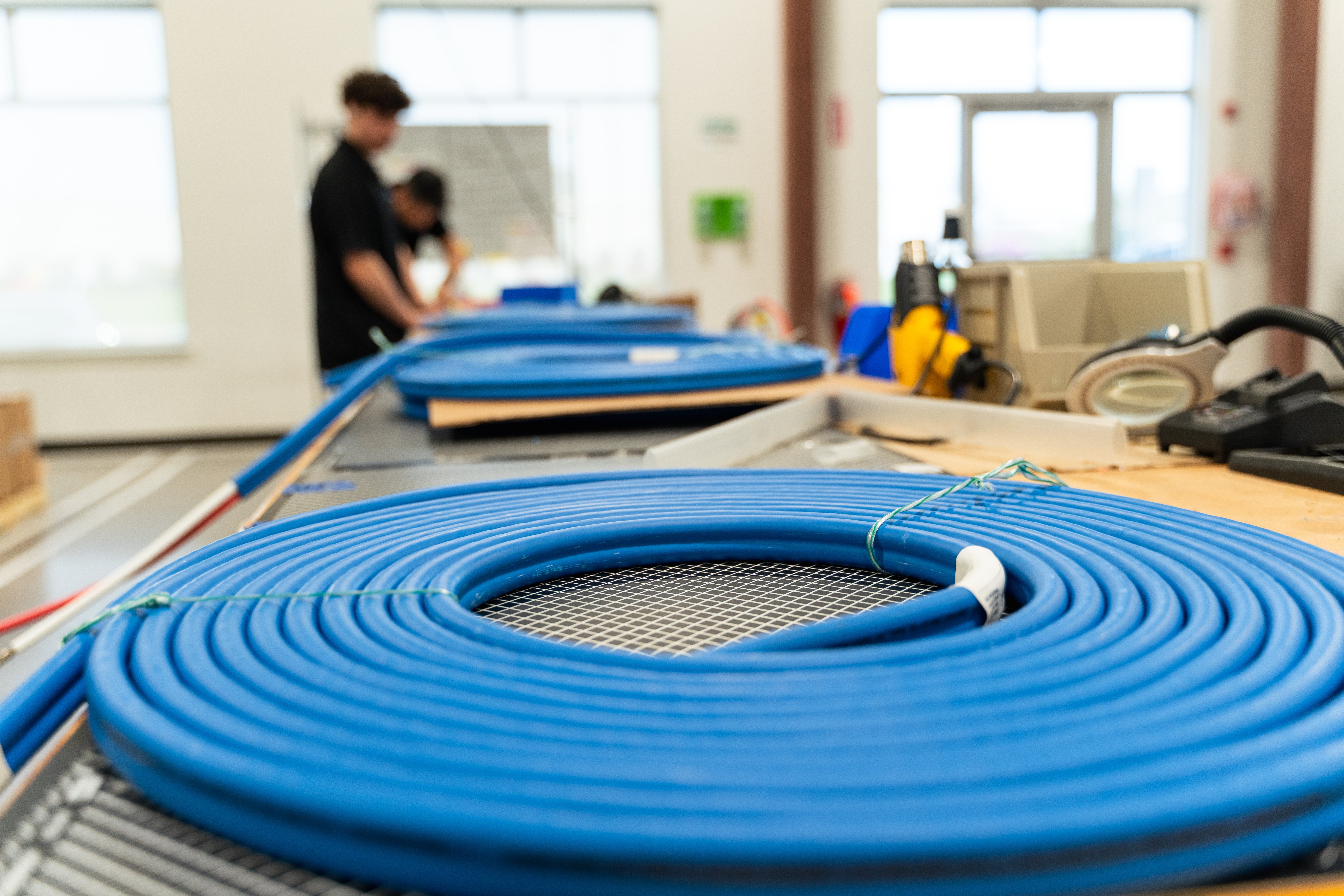
Top suppliers:
Overview of Cable & Wire Labels
Industrial marks and labels might be small, but they can have a huge impact on your application. An effective and consistent labeling and signage system can make your operation:
- More productive
- More profitable
- Less of a hassle
- Safer & more secure
Those benefits are easy enough to understand, yet the seemingly endless types of labeling solutions can overwhelm a sourcer at first glance. While all wire marking solutions have the same universal benefits, each type best meets a certain range of applications. Selecting the best wire and cable labels comes down to safety, compliance, termination location, and material needs.
Types of Industrial Cable & Wire Labels
While there are many wire identification options out there, industrial electrical cable and wire markers fit into three main types:
Type | Pros | Cons | Use Cases | ||||
Heat-Shrink Sleeves |
|
|
High-temperature environments; control panels; outdoor use | ||||
Wrap- Arounds |
|
|
Indoor environments; temporary labeling | ||||
Flags & Tags |
|
|
Situations needing quick identification; accessible panels |
Heat-shrink sleeve labels slip over the cable before termination. They allow users to slide them along wires or cables for optimal placement. Once you apply heat to affix the label, you’re stuck with that location.
The heating process shrinks the sleeve to a predetermined size, typically 1/3 to 1/6 of its original diameter. For industrial labeling needs, it's crucial to select the appropriate diameter and type of sleeve. You can cut the length to size prior to heating.
Wrap-around labels are for use after termination. These labels are adhesive and wrap around the entire diameter of a wire. Available in preprinted and stand-alone forms, the material is typically clear polyester or vinyl, with a small, white area for marking by hand or printer. Special types of wrap-arounds are available for adding moisture protection, repurposability, or readability.
Flags can go on cables before termination to help ID them during installation, or after termination to provide permanent labeling. The material partially wraps around the cable and sticks to itself, forming a flag-like extension. This design is particularly useful for identifying cables in dense or hard-to-reach areas.
Tags also work either before or after the cable’s termination. The material makeup can be either plastic or metal. Tags’ main difference from cable flags is that you have to attach them with a tie or similar fastener. On the plus side, this makes them more durable for permanent labeling situations.
Circuit Breakers
Top Criteria for Circuit Breakers | |
Voltage rating | Current rating |
Interrupting capacity | Corrosion resistance |
Frequency | Installation & maintenance |
Tripping current level adjustment ranges | Number of poles |
Testing |
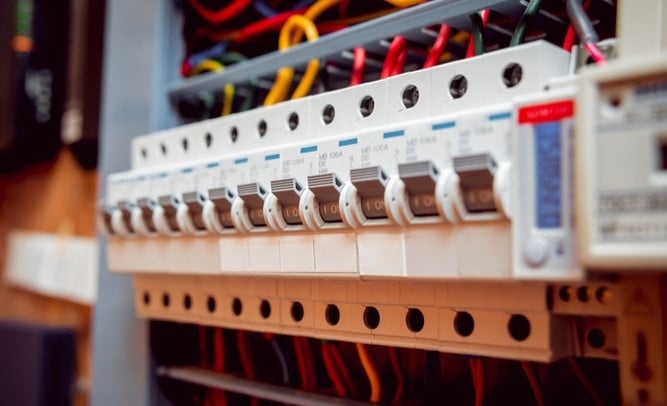
Top suppliers:
Overview of Circuit Breakers
The industrial circuit breaker is the gatekeeper of many critical electrical products.
This component acts as a protective switch for passing electrical currents. When it detects a fault, the circuit breaker interrupts the current’s flow, isolating the input and output voltages from contacting one another. It’ll stay open until the user resets the trip.
Electrical prowess is the first order of business in comparing circuit breakers.
- Voltage rating must match your system’s voltage levels to remain safe and efficient. The rating depends on the protector’s insulation thickness (usually 100% in grounded systems and 133% in ungrounded systems).
- Current rating must also align with system requirements; heavy-duty needs may force you to rule out miniature or residual current breakers. A too-low current rating will cause unwanted tripping and downtime; a too-high rating may allow the circuit to overheat and catch fire.
- Interrupting capacity must be equal to or greater than the fault current your system could produce at the breaker’s location. Large operations value this spec because a high capacity allows them to function safely and avoid tripping the breaker repeatedly.
- Frequency of a circuit breaker should match the frequency of the electrical system to ensure efficiency and functionality. Using a 50 Hz breaker in a 60 Hz system could reduce the system’s power rating, damage the breaker, or even damage the system it’s “protecting.”
There are also several physical and environmental traits that factor into a breaker’s usefulness – read about them at the button below.
Types of Circuit Breakers
There are many ways to categorize circuit protectors – an obnoxious and confusing number of ways, to be honest. We recommend you start by considering the interruption medium.
These are the main types of industrial circuit breakers by interruption method:
Type | Pros | Cons | Use Cases | ||||||
Air |
|
|
Low to medium voltage; indoor installations | ||||||
Oil |
|
|
high voltage Outdoor units | ||||||
SF6 |
|
|
High voltage; compact areas | ||||||
SF6 |
|
|
Medium voltage; indoors & outdoors |
This categorization reflects the different tech used to extinguish the arc during the current interruption. The method directly impacts the breaker’s specs, performance, and plausible uses.
- Air circuit breaker (ACB): Used air to extinguish the arc
- Vacuum circuit breaker: Electricity can’t pass through a vacuum!
- SF6 circuit breaker: Uses sulfur hexafluoride gas to cool and quench the arc, and is a popular replacement for environmentally risky oil breakers
- Oil circuit breaker: Uses oil to extinguish the arc.
Fuses
Top Criteria for Fuses | |
Voltage rating | Current rating |
Interrupting capacity | Corrosion resistance |
Current-limiting ability | Installation & maintenance |
Speed | Need for holder |
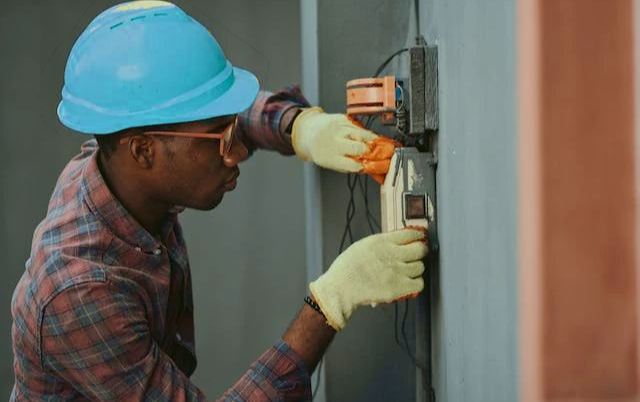
Top suppliers:
Overview of Fuses
Industrial fuses come in so many easy-to-find types that it’s common for two to look nearly identical. Problem is, they might function just differently enough to be dangerous. Worst-case scenario, this guessing game can lead to selecting the wrong fuse, putting people and expensive equipment at risk.
At least voltage rating is easy enough to nail down – all fuses are straight voltage-rated. A straight voltage rating means you can use the fuse in circuits with a nominal voltage up to its rated value between any two conductors. For example, an industrial fuse with a rating of 250 V is OK to use in a circuit where the line-to-neutral or line-to-line voltage is 250 V or less.
Overall, some buyers feel that fuses are simpler or more consistent sourcing options compared to mechanical overcurrent devices. If you’re not sure, ask a distributor with technical product expertise.
Interestingly, sizing an industrial fuse means taking both electrical and physical needs into account. The fuse’s voltage rating must comfortably exceed your application’s current level, or else it’ll blow needlessly. However, it must also fit inside the assembly without crowding other components, which could lead to heat buildup and other performance issues.
Start by calculating the maximum and minimum fuse ratings:
- Wattage / voltage = max fuse rating (amps)
- Max fuse rating * 1.25 = minimum fuse rating
Don’t use any so-called “10% rule.” Size the fuse for safety first, and keep the value well above the expected load. Balance this against the internal dimensions of the fuse’s intended home. Spec a fuse to a plausible maximum load to avoid overspending.
Finally, don’t forget to watch for these other factors when sourcing fuses:
- Current rating should be slightly above the circuit's normal current, but below the wire’s or device’s current capacity.
- Interrupt (breaking) capacity will need to be high if you’re working with a high-voltage application.
- A current-limiting fuse reduces the duration and magnitude of a fault current, minimizing equipment damage and protecting people.
- Corrosive & environmental threats are avoidable by picking a fuse with the right temperature rating, coating, fire rating, or build for your application.
- Speed comes in four tiers – ultra-rapid, fast-acting, time-delay, and dual-element – and should be selected based on how quickly you need circuit interruption.
Types of Fuses
Most buyers categorize fuses one of three ways: build, application, or operating characteristics. While it's tempting to go for the cheapest option in a given category, remember that a fuse is a safety device.
Type | Pros | Cons | Use Cases | ||||
Fast-Acting |
|
|
Where precise protection is critical (consumer electronics, power supplies, medical equipment) | ||||
Time-Delay |
|
|
Motors & transformers that draw high inrush currents | ||||
High Rupture Capacity (HRC) |
|
|
Industrial power systems | ||||
Current- Limiting |
|
|
Transformers, capacitors, & other critical power equipment | ||||
Thermal |
|
|
Over-temperature protection in household appliances (heaters, dryers) | ||||
Resettable (PTC) |
|
|
Consumer electronics, automotive, USB peripherals | ||||
Glass |
|
|
Automotive, low-current electronic applications | ||||
Ceramic |
|
|
Meeting high performance & durability needs (industrial machinery, auto, certain appliances) |
No matter the type of fuse, you’re buying it for one-time use. Once it does its job – stopping a current from harming the circuit – you’ll have to replace it.
PLC (Programmable Logic Controllers)
Top Criteria for PLCs | |
Features | Mechanical durability |
Ease of use | Corrosion resistance |
Communication protocol | Installation & maintenance |
Security | Futureproofing |
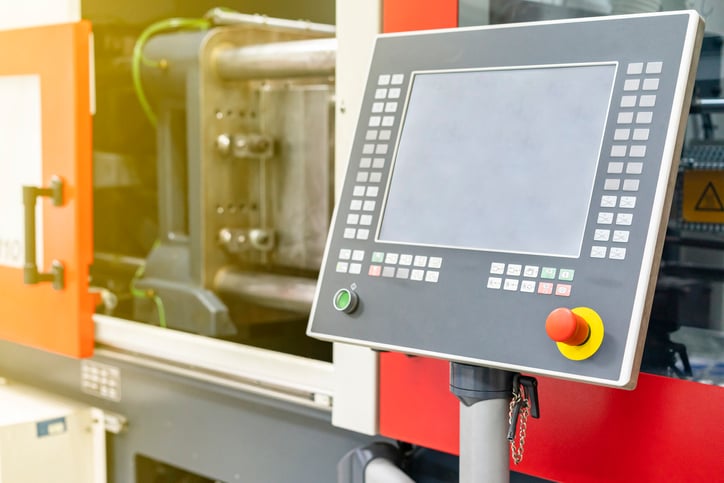
Top suppliers:
Overview of PLCs
A programmable logic controller (PLC) is the heart of many an industrial process. Think of it as a heavy-duty computer – one that’s been adapted to control a machine, assembly line, or robot. The difference between an industrial PLC and your old Lenovo laptop is that reliability, easy programming, and advanced fault diagnosis are must-haves rather than nice-to-haves.
The PLC selection process should start with a drawing of the parent process or equipment. A good schematic identifies all field devices and physical requirements for hardware locations. It can also help determine the number of analog and discrete devices you’ll need.
Unlike most components on this page, PLC choice largely comes down to the features you need vs. the price you want. Key parameters here include:
- Number of I/Os – A higher count typically means the PLC can manage bigger and more intricate operations
- Processing speed – Does your application require real-time decision making and rapid response to changing conditions?
- Power requirements – Impacts compatibility with existing systems, energy use, & the need for extra power supply units
Unsurprisingly, the more impressive a PLC is in these areas, the higher its price.
As you investigate PLCs, there are several other traits that deserve your attention.
- Software should be engineer-friendly. Check out the simplest options first, as 80% of the average software’s features are rarely or never used. User comfort level with the device impacts the speed of development, troubleshooting, and maintenance.
- Present- and futureproofing means guaranteeing compatibility with both today’s and tomorrow’s system. Certain controllers don’t play well with others, so save yourself the time and rework by getting this right the first time. You save even more time and money by buying a scalable system that allows for extra input/outputs, expansion racks, and easy integration of new interfaces.
- Durability still matters, just like with other electronic components on this list. Controllers most often fail because the buyer exposes them to moisture, extreme temperatures, harmful substances, EMI, or vibration. If one or more of those is inevitable in your end-use environment, find a PLC with the appropriate material build and compliance ratings.
Types of PLCs
Most people in the industry categorize logic controllers by size and complexity. Your choice will be incredibly dependent on what you’re trying to control or automate, and how complex that process is.
Type | Pros | Cons | Use Cases | |||||
Micro |
|
|
Small-scale automation, simple machine control, home automation | |||||
Compact |
|
|
Standalone machines, small to medium processes, where space is a constraint | |||||
Modular |
|
|
Medium to large manufacturing processes, highly customized systems | |||||
Rack- Mounted |
|
|
Large industrial applications, complex control systems | |||||
Process Controllers/PACs |
|
|
Complex industrial processes, integration of process and control |
While both micro and compact PLCs are used for smaller applications, micro PLCs are the more basic option, providing just enough functionality for the simplest of tasks. Compact PLCs strike a greater balance between functionality and size.
PACs (process automation controllers) are not merely another type of PLC. They’re more advanced and versatile, using C or C++ as a programming interface vs. the simpler ladder logic of standard PLCs.
Relays
Top Criteria for Relays | |
Voltage rating | Heat, flame, & cold resistance |
Current rating | Mechanical durability |
Speed | Installation & maintenance |
Contact configuration | Coil voltage |
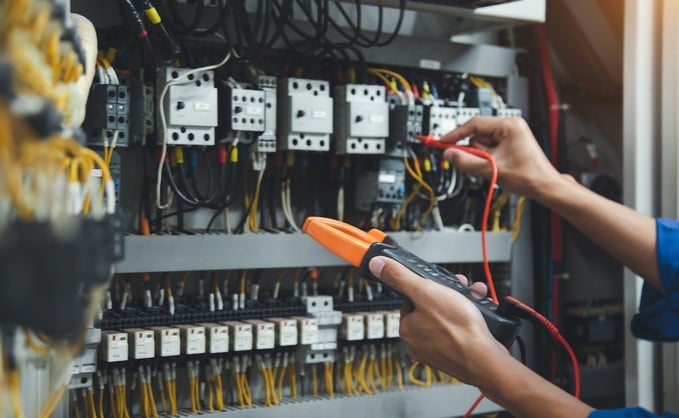
Top suppliers:
Overview of Relays
Industrial relays are versatile electronic components that are just as handy for simple circuits as they are complex ones. If you use them in place of switches or high-amp wiring (when appropriate), you can save money and assembly space.
As is often the case, both electrical and physical traits matter when selecting a relay. Understanding a few basics will set you off on the right path.
- Mounting type will impact the space available in the installation, and how much heat buildup the relay will contribute.
- Switching type can be either normally open (NO), normally closed (NC), or changeover (CO). This impacts the relay’s speed, ability to handle current, durability, and more.
- Surge current durability refers to input surge current (or inrush current), the maximum amperage a relay contact can withstand for a specific load type. To keep your system safe and reliable, compare any potential relay’s maximum surge current rating with the application’s expected inrush current. Leave a little margin for error, just in case.
- Voltage rating is different on a relay’s contact side vs. its coil side. This is because the relay needs to switch and handle the load current, which may have a different voltage requirement than the control circuit. Most industrial-grade relays come in 24-, 48-, 120-, and 240-volt options.
- Operating environment factors that most affect relay performance include hot, cold, humidity, corrosives, and vibration. Specifically, trouble areas include manufacturing, oil, gas, and mineral applications.
- Isolation between control & load circuit helps protect sensitive control circuits (and people) from electrical threats on the load side. To meet this relay selection guideline, buy a product with enough dielectric strength and insulation to stop interference or damage.
- Multiple contacts are valuable in a relay if you want simultaneous control of several circuits or a specific sequence of operation. It’s more efficient to do this with a single multicontact relay vs. several single-contact ones.
Types of Relays
Each electric or electrical project might require a different type of industrial relay, contact configuration, or expectation for switching time.
Start your hunt by figuring out which type of relay provides the best combination of these and other factors important to your assembly. The three big ones are:
Type | Pros | Cons | Use Cases | |||||
Electromechanical Relays |
|
|
General industrial control, automotive, electrical machinery | |||||
Reed Relays |
|
|
Telecom, medical, & testing equipment | |||||
Solid-State Relays (SSR) |
|
|
Heating regulation, lighting control, areas needing silent operation |
Electromechanical relays are a well-understood and reliable technology great for general use. Reed relays make sense when you need to combine fast switching in a low-power application. Solid-state relays are what you’ll need when the job requires precise and rapid control.
The more powerful the product, the more durable it is, too. Reed relays have a longer lifespan than electromechanical relays. However, SSR relays beat them both by virtue of having no mechanical parts to begin with.
Sensors
Top Criteria for Sensors | |
Energy & voltage | Accuracy & sensitivity |
Size & mounting | Corrosion resistance |
Speed | Heat, flame, & cold resistance |
Resolution & range | Output signal & compatibility |
Linearity | Connectivity |
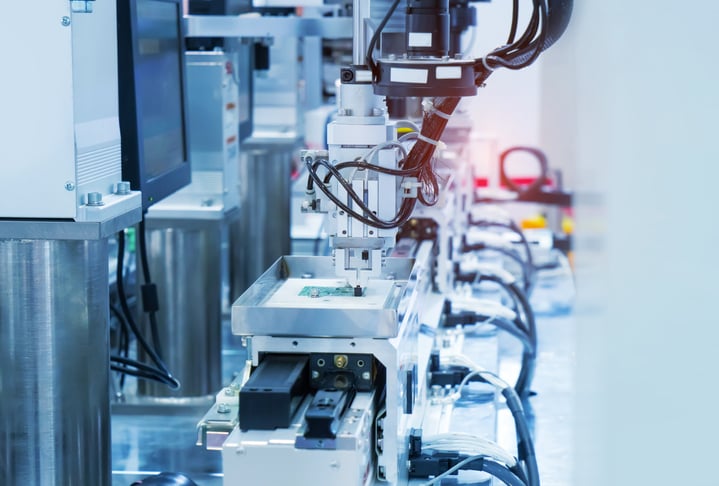
Top suppliers:
Overview of Sensors
Industrial sensors are all about the numbers. They measure data such as temperature, pressure, and flow rate, making sure a system is running smoothly and safely.
In many operations where reliability rules, knowing how to choose a sensor is not just an option. It’s a necessity for anyone looking to max out the full potential of their electronic system.
The ability to detect and read measurement criteria is an obvious buying criteria for a sensor, but there are many others.
- Compatibility is based on output signal, voltage level, current requirement, and communication protocol. The sensor’s choice of analog or digital output, for example, determines whether it can actually communicate with your existing system.
- Size and mounting method will impact the sensor’s stability on the assembly, which in turn influences its accuracy. You may need specific mounting hardware to keep the sensor in place, especially if the end-use area will include vibration or other physical stressors.
- Energy and voltage requirements must match your power supply capabilities and not overload the surrounding grid. Does your potential sensor have a voltage level that the system can currently accommodate? Does it chew up battery life?
- Speed comes in the form of response. Is it important for your industrial sensor to give a quick first reading? Is it OK if your sensor has a long recovery time before it can take a second reading?
- Environmental durability is a key buying criteria because sensors are, well, sensitive. Physical threats to account for include vibration, wear, pressure, and debris (i.e. dust). Chemical threats include extreme temperatures, water, corrosive substances, and UV light.
- Connectivity is key in today’s warp-speed world. Some sensors require wired connections to a network, while others can transmit data wirelessly. Advanced products can send data to IoT networks or even your industry-specific control system.
Types of Sensors
Industrial components tend to come in many varieties and categories, but sensors might take the cake. Let’s attempt to break them down as simply as possible:
Type | Pros | Cons | Use Cases | |||||
Position Sensor |
|
|
Used in robotics for precise movement, automotive systems for vehicle control | |||||
Pressure Sensor |
|
|
HVAC, auto braking, monitoring industrial processes | |||||
Temperature Sensor |
|
|
Climate control systems, electronics manufacturing, process monitoring | |||||
Humidity Sensor |
|
|
Building management, agriculture for soil monitoring, meteorology | |||||
Force Sensor |
|
|
Touch-sensitive devices, industrial automation, scales | |||||
Vibration Sensor |
|
|
Fault diagnosis in machinery | |||||
Motion/ Proximity Sensor |
|
|
Fault diagnosis in machinery | |||||
Motion/ Proximity Sensor |
|
|
Security systems, lighting, touch-free UIs | |||||
Flow Sensor |
|
|
Water management, chemical processing, fuel distribution | |||||
Level Sensor |
|
|
Inventory management in storage tanks, safety systems, process control |
As you can see, sensor types are more application-dependent than your average electronic component. For example, pressure sensors are for measuring liquid and gas, while force sensors are for mechanical measurement.
From there, pros and cons often vary by specific product. Some force sensors can measure in multiple directions. Along those lines, some flow sensors can measure flow direction as well as rate, but their performance can drop if there’s particulate matter in the fluid. And certain types of level sensors won’t work as well if there’s foam or vapor present above the liquid.
In the world of temperature sensors, many types are available (i.e. thermocouples, RTDs, thermistors) to suit different accuracy and range needs. Advanced models of vibration detectors can differentiate between normal vibrations and those signaling potential failures. And high-end motion and proximity sensors can tell the difference between human and non-human movement.
Some level sensors offer contactless measurement, reducing wear and contamination risks. In the pressure sensor market, some come with protective measures so that overpressure isn’t a risk.
Of course, all industrial sensors must provide some level of ability to work in rugged environments without losing accuracy. Regardless of purpose, industrial sensors typically require regular calibration, so don’t fret if that’s the case.
Terminal Blocks
Top Criteria for Terminal Blocks | |
Voltage rating | Number of poles |
Current rating | Corrosion resistance |
Futureproofing | Installation & Maintenance |
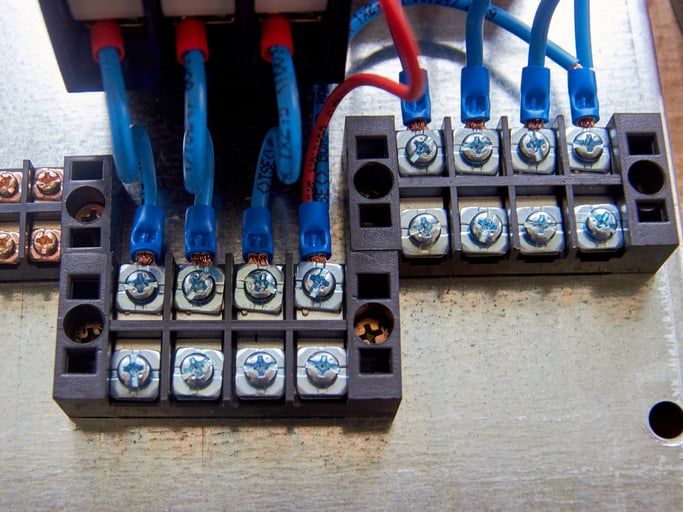
Top suppliers:
Overview of Terminal Blocks
Terminal blocks are the professional’s alternative to soldering or taping, offering a convenient way to connect and terminate wires.
The most popular mounting solution for terminals is a DIN rail. This tends to simplify wiring setup and save space in the enclosure.
Along those lines, accessibility is an important feature in terminal block installations. In addition to keeping terminal footprint minimal, consider using screws as your fastening method. These connections are easier to modify and add an element of futureproofing to your assembly.
Besides the usual comparison points, a common way to start your terminal block hunt is to check how many circuits the assembly needs. This determines the number of poles the block must have.
(Tip: With terminal blocks, it’s entirely possible your engineering team will care about only one criteria: compatibility. Many prefer that all terminal blocks in an installation come from the same manufacturer.)
Types of Terminal Blocks
There are many ways to classify industrial terminal blocks:
- Connection method
- Wire-securing method
- By function
Let’s focus on the most common way – connection method. You can learn about the other categories at the button further below.
Type | Pros | Cons | Use Cases | |||
Barrier Strips |
|
|
Power supply applications, control panels, automotive systems | |||
IEC PCB Mount |
|
|
Electronic equipment, instrumentation, & consumer goods that need direct PCB mounting | |||
Feed- Through |
|
|
Electrical distribution, industrial control, transportation systems | |||
Edge Connector |
|
|
Computer systems, servers, & network equipment for modular board connectivity |
Barrier strips (aka single-row) terminal blocks are extremely common in the U.S. They consist of three main parts: a plastic or thermoplastic body, multiple terminals, and barriers separating them. A screw or clamp connects the wires, and sometimes a small enclosure or lid protects them.
IEC PCB mount (aka Euro style or wire-to-board) terminal blocks are a staple of, you guessed it, PCBs (printed circuit boards). They work by placing bare wires in the module, where housing and a clamp secures the strands. PCB terminal blocks can be single-, dual-, or multilevel (usually three or four) structures. You can mount PCB blocks either through the board or via pluggable pin strip mounting.
Feed-through terminal blocks feature two input sides (one on each side), where two distinct wires are fed through the housing. They use the screw-in method of connection, coming with predrilled holes. They come in single, dual, or multilevel modules.
Edge connector terminal blocks accept a circuit board edge into their housing. Putting them together matches the copper traces and screws the block into an enclosure. This means the block only needs one discrete female connector.
By understanding how each type works, you can ensure safe connections, make maintenance and troubleshooting easier, and streamline the overall assembly.
Vehicle Lighting – Industrial
Top Criteria for Vehicle Lighting | |
Mechanical durability | Heat, flame, & cold resistance |
Energy efficiency | Corrosion resistance |
Brightness & quality | Installation & Maintenance |
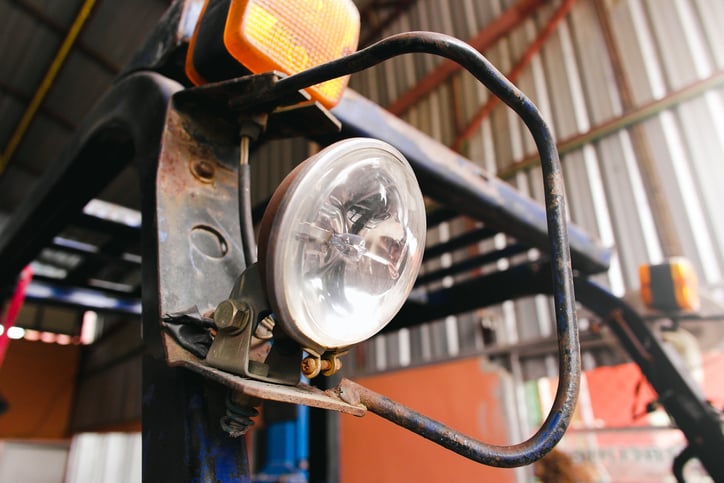
Top suppliers:
Overview of Industrial Vehicle Lighting
technology improvements and changing needs have shifted the methods of lighting used in industrial situations. With the variety of lighting needs in a vehicle, and the investment each type entails, it’s important to understand all project requirements before buying.
Here are some more details to watch for as you choose the best OEM work lights for your vehicles:
- Energy efficiency: Commercial vehicles and equipment often operate for extended periods, making them major energy eaters.
- Durability: Unlike residential rides, industrial and commercial vehicles may face frequent exposure to caustic chemicals, heavy mechanical wear and tear, and extreme weather.
- Brightness & light quality: Industrial workplaces have established lighting standards. From field maintenance to excavation, the quality and brightness of light must match these standards. Nuances to watch out for in your application include color rendering, as well as focus vs. diffusion.
- Fixture type: Remember, the product you’re buying is part of a larger assembly. Without the right mounting setup, it may become out of position or unstable in a vibratory or high-movement use case. Also, if the connector doesn’t properly support the light fixture, it might interfere with the vehicle’s electrical system. Make sure the installation kit includes all necessary wires, adapters, and plugs.
- Safety: All vehicles have strict regulations and standards for safety. Installing work lights that provide long-term solutions – not just the cheapest quick fix – will keep your company away from related fines and penalties.
Types of Industrial Vehicle Lights
Type | Pros | Cons | Use Cases | ||||||
Incandescent |
|
|
Older vehicles, interior lighting | ||||||
Halogen |
|
|
Headlights & spotlights | ||||||
LED |
|
|
Headlights, brake lights, interior lighting, & much more |
Each common method of commercial vehicle lighting works a little differently:
- Incandescent lighting: Uses electricity to heat a filament in a bulb filled with oxygen-free gas, generating light
- Halogen lighting: A type of incandescent light that uses gas to create a brighter light
- LED lighting: Uses a light-emitting diode (LED) to generate brightness when electricity passes through it
Unlike most other electronic components, OEM lighting types have clear-cut levels of quality. Incandescent products come cheap for a reason, LEDs are expensive but excellent, and halogen lights are in the middle. Sure, project-specific factors will occasionally influence your choice, but buying vehicle lighting mostly comes down to quality vs. budget.
Manufacturer Resources for Your Electronics Supply Network
Need to know where to buy electronic components safely and swiftly in today’s ultracompetitive market?
As you window-shop, stay sharp for signals of whether the manufacturer’s size actually equates to quality.
In some ways, identifying the top component manufacturer comes down to your application’s specifics and level of complexity. Will the component be responsible for operating a 10-ton lift over workers’ heads? Will it provide data feedback from a commercial airplane? In mission-critical work, a brand you trust is worth its weight in copper
(Tip: In some assemblies, your engineers may prefer that all of a certain component [i.e. terminal blocks] come from the same manufacturer. It’s a compatibility thing.)
If it’s too close to call between two candidates, go with the company that’s got history on its side. A proven, financially stable operation is less likely to leave you holding a faulty batch with nobody to answer for it.
There are many good electronics manufacturers out there beyond the few highlighted for each component above. For a fuller list, see our supplier page:
Distributor Resources for Additional Electronics Supply Solutions
If the totality of electronic parts sourcing – predicting shortages, managing stock level, and getting fair pricing – is overwhelming you or your team, there’s help available.
Working with a distributor can relieve many symptoms of a bad electronics sourcing experience. Depending on the distributor’s skill set and supplier network, it may offer a wide range of cost-saving services and features:
What Can a Distributor Do for You? |
|
Value-Adding Benefits | Value-Added Services |
Discount pricing & favorable terms | Inventory management |
Better access to rare or high-demand parts | Warehousing |
Order volume flexibility | Supply forecasting |
Recommend part replacement or assembly redesign | Kitting, packaging, labeling & respooling |
If you’re not quite ready for a distributor, there’s another learn-on-your-own resource available. The free Guide to Electronic Sourcing will help you:
- Identify when your supply chain needs a change
- Mitigate the impacts of war, weather, & high demand
- Vet distribution & direct-buy options