Careers
At Simcona, our team plays a key role in our success. People who succeed at Simcona all have something in common – they are customer-centric, forward thinkers, and passionate about what they do. Headquartered in Rochester, New York, we strive to build an inclusive environment that empowers everyone to do their best work.
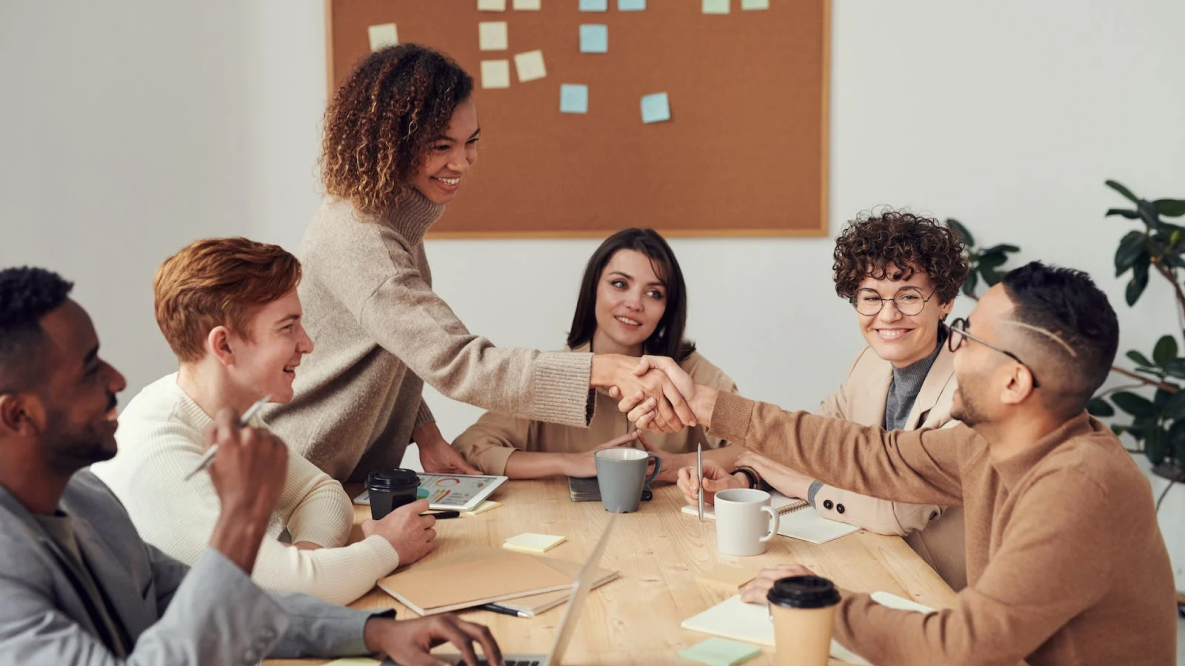
Financial
401(k) plans & Profit sharing plan
Vacation, national holidays, and personal days
Paid family leave
Life insurance
Short-term & Long-term disability plan
Retirement planning assistance
Health
Medical insurance plan
Prescription drug coverage
Dental insurance coverage
Vision insurance coverage
Employee assistance program
Free preventative care
Training & Development Opportunities
Learning doesn’t stop once you have the job – it’s key to your personal and career progression. Career benefits for you may include…
- On the job training
- Development opportunities
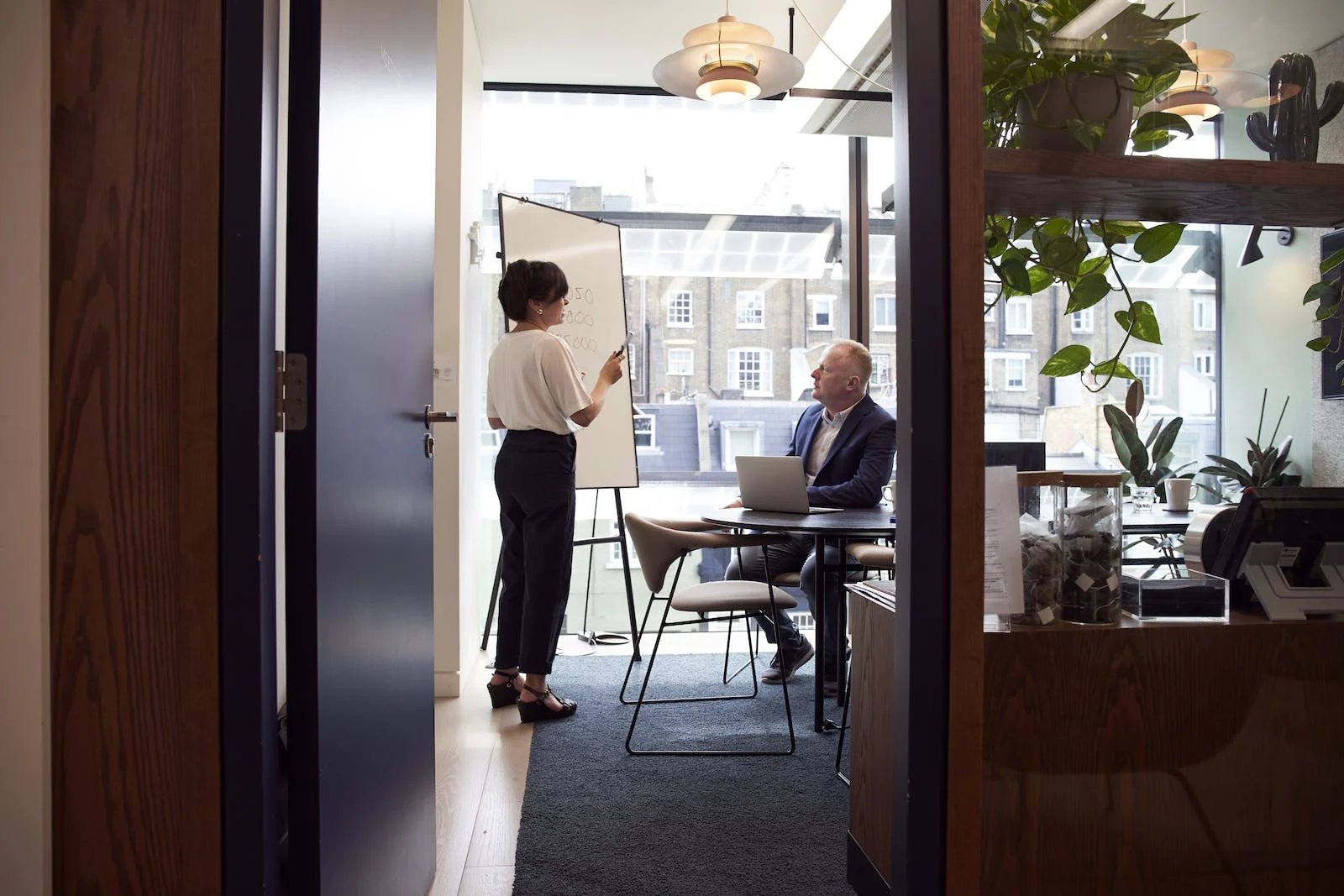
Open Positions
Production Supervisor Position
Pay Range:
- $65,000 - $70,000
Job Summary:
Production Supervisor for Electrical Panel Manufacturing (Production Supervisor) will oversee the daily operations of Electrical Panel Manufacturing team to deliver products that are defect-free and according to agreed-upon schedules.
The Production Supervisor is responsible for production labor, that they have the skills, tools, work environment, and support required to perform efficiently and effectively to meet the goals and objectives of each project.
In addition, the production labor must comply with applicable policies, procedures, quality standards, workmanship standards, and professional behaviors.
The Production Supervisor facilitates ideas from the production labor and collaborates with management, operations, and engineering to implement continuous improvements in safety, quality, delivery, and operating costs.
The Production Supervisor reports to the VP of Operations.
Responsibilities & Duties:
- Accomplishes manufacturing results by communicating job expectations; planning, monitoring, and appraising job results; coaching, counseling, and disciplining employees; and initiating, coordinating, and enforcing systems, policies, and procedures.
- Schedule labor resources in the most efficient manner based on skills sets and completing jobs within the time standard presented by the Planning Manager.
- Maintain workflow by monitoring and upgrading processes, setting processing variables, observing control points and equipment, monitoring personnel and resources, studying methods, implementing cost reductions, developing reporting procedures and systems, facilitating corrections to malfunctions within process control points, and initiating and fostering a spirit of cooperation within and between departments.
- Collaborate with operations, receiving, and warehouse staff to make sure materials are distributed to work areas in a timely and complete manner.
- Communicate to operations, engineering, and management issues that negatively impact performance (waste) in an urgent, clear and concise manner.
- Maintain quality service by establishing and enforcing production standards.
- Ensure operation of equipment and tools by calling for calibration, repairs, and proper use.
- Manage labor attendance, weekly time sheets for payroll, personal time off (PTO) including planned and unplanned absences.
- Help implement and maintain a 6S work environment
- Help maintain the company’s ISO9001:2015 certification
- Assure that the production facility is a safe environment for employees. Record and report to the Director of Operations and Engineering Manager all safety violations, near-misses, and injuries.
Qualifications & Skills
These topics will be measured by observations by management, reported incidents, on-time delivery, accuracy of data, and 360-degree surveys.
- Supervisory:
- Commands respect of employees
- Demonstrable team building, decision-making and people management skills
- Coaching and problems solving
- Ability to delegate as required to maintain a high work output
- Outstanding organizational skills with a high attention to details.
- Leads efficiency
- Ability to multi-task and effectively track project deliverables.
- Technical
- Ability to read blueprints, technical documents, and manuals
- Analytical skills – problem solving, failure analysis, DMAIC
- Advanced skills with Microsoft Office Products
- Proficient understanding of mechanical mathematics
- Knowledge of safety, quality, productivity, demand creation, inventory, and stewardship processes in a manufacturing environment
- Strong verbal and written communication skills required
Working Environment
While performing the duties of this job, the employee frequently works near moving mechanical parts, and high-speed equipment; Must be able to see, grasp hold, walk, sit, reach, climb, bend, and stretch, lift up to 40 lbs. Will spend considerable time in the production environment where temperatures fluctuate, floors may be wet, and noise is a constant factor in the work environment.
This job description is not designed to cover or contain a comprehensive listing of activities, duties or responsibilities that are required of the incumbent. Duties, responsibilities, and activity may change, or new ones may be assigned at any time with or without notice.
Measure of Success
Currently in place:
- Daily timecards of activities including time, panel, and activity
- Every employee that modifies a panel must sign the work order traveler for that panel, establishing and adding-to a record of the work performed
- Estimated versus actual labor hours entered into DBA ERP
- Reports are generated from DBA ERP on labor per panel, created for closed jobs
- Productivity, revenue per employee and gross margin per employee
Measures to be collected include but may not be limited to the following:
- Quality, defect per panel builder, tracked for each panel builder.
- Defect may be discovered before or after shipping, success is zero defects
- Defects by time discovered, time produced, production labor involved in creating and detecting the defect, and root cause in collaboration with engineering and operations
- Associate panel builder with work order and serial number
- Scrap and rework
- On-time delivery to committed schedules
- Time to build, tracked for each panel builder
- 360-degree survey of direct reports and peers
Confidentiality
The Production Supervisor has access to confidential company information relating to vendor/customer relationships, products, organizational growth strategies and company strategic plans. A high degree of confidentiality is required.
Back to Open Positions